Breathing easy while welding isn’t just about comfort; it’s about safety. Welding creates tiny particles and fumes that can be harmful if inhaled. Choosing the right respirator, like a 3M particulate welding respirator with an exhalation valve, is crucial. Whether you need a disposable welding respirator like an N95 or a more reusable half facepiece option, understanding the differences helps protect your lungs. This guide breaks down everything you need to know about selecting and using a particulate welding respirator, including popular 3M™ models like the 8212 (P95), ensuring you get a secure seal against non-oil based particles and dangerous welding fumes. We’ll explore why the right respirator is non-negotiable for any welder.
As someone who runs a factory producing essential medical consumables, like high-quality Medical surgical face masks and sterile supplies, I, Allen, understand the importance of reliable protection. My company, ZhongXing in China, focuses on creating dependable products – from cotton swabs to gauze bandages – meeting strict standards like ISO 13485. We export globally, serving clients like Mark Thompson in the USA, who demand quality and compliance. While we specialize in medical disposables, the core principle remains the same: protecting people from airborne hazards. This requires understanding filtration, fit, and the specific needs of the environment, whether it’s a hospital or a welding workshop. This article dives into the specifics of welding respirators, particularly particulate respirators designed to handle fume exposure, drawing parallels from the stringent quality control we apply to our own medical products.
Why is a Specialized Welding Respirator Necessary? Understanding the Dangers of Welding Fumes.
Welding might look like just sparks and bright light, but it creates a hidden danger: welding fumes. These aren’t just smoke; they are a complex mix of tiny metal particles and gases released when metal is heated to high temperatures. Breathing these fumes in can be really bad for your health, both right away and over the long term. Short-term exposure can cause things like dizziness, nausea, or "metal fume fever," which feels like the flu. Think of it like your body reacting to something harmful it just breathed in.
Over time, the risks are even more serious. Continuous exposure to welding fumes, especially those containing metals like manganese, chromium, or cadmium, can lead to severe lung problems, including chronic bronchitis, asthma, and even lung cancer. Neurological problems are also a concern with certain types of fume exposure. That’s why using effective respiratory protection isn’t optional; it’s essential. A simple cloth mask or even a basic dust mask won’t cut it. You need a specialized welding respirator, often a particulate respirator, designed specifically to filter out these dangerous airborne particles and metal fumes. Protecting your lungs means choosing the right respirator for the specific type of weld work you’re doing.
Think about the standards we adhere to for medical supplies. A simple cotton ball isn’t designed to stop viruses, just like a basic mask isn’t designed to stop microscopic metal particles from welding. You need equipment engineered for the specific hazard. Occupational Safety and Health Administration (OSHA) sets limits (Permissible Exposure Limits or OSHA PEL) for welding fumes, but the best approach is always to minimize exposure as much as possible using the correct respirator.
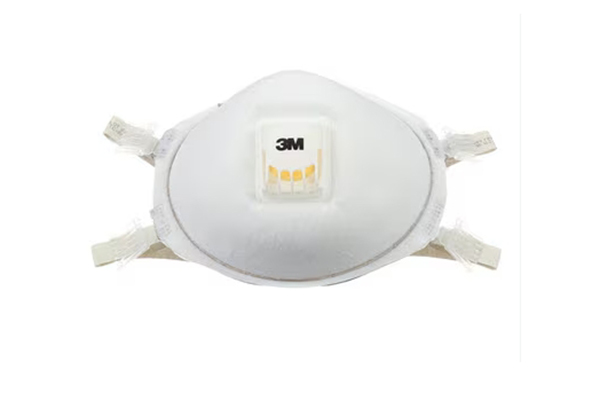
What’s the Difference Between Disposable and Reusable Respirators for Welding?
When choosing respiratory protection for weld tasks, one of the first decisions is whether to go with a disposable respirator or a reusable one. Both have their pros and cons, and the best choice often depends on the frequency of welding, the environment, and personal preference. A disposable respirator, like many common N95 models, is designed for single or limited use. You wear it for a shift or until it gets dirty, damaged, or hard to breathe through, and then you throw it away. They are often lightweight and convenient, requiring no cleaning or maintenance. Many disposable welding respirators come with features like an exhalation valve for easier breathing and flame resistant layers.
Reusable respirators, on the other hand, typically involve a facepiece (often a half facepiece or full facepiece) made of silicone or rubber, combined with replaceable cartridges or filters. The facepiece itself can last a long time with proper cleaning and care, and you only replace the particulate filter or cartridges when needed. This can be more cost-effective in the long run for frequent welders. Reusable respirators often provide a better secure seal due to more robust faceseal designs and adjustable head straps. Some reusable respirator systems also offer flexibility, allowing you to attach different types of filters for various hazards, including particulate protection (P95, P100), organic vapor filtration, or even acid gases, using a bayonet connection system.
The choice boils down to convenience versus long-term cost and versatility. For occasional weld jobs, a quality disposable respirator like a 3M™ N95 or P95 might be sufficient. For daily welding, especially in environments with heavy fume concentration or multiple hazards, investing in a comfortable, well-fitting half facepiece reusable respirator with appropriate particulate filters often makes more sense. Both types require a proper fit test to ensure they provide the intended level of respiratory protection.
Decoding NIOSH Ratings: What Do N95, P95, and P100 Mean for Welders?
You’ll see letters and numbers like N95, P95, and P100 on respirators. These aren’t just random codes; they are ratings from the National Institute for Occupational Safety and Health (NIOSH), a US agency that tests and approves respirators. Understanding these ratings is key to picking the right respirator for welding. The letter tells you about resistance to oil aerosol particles:
- N: Not resistant to oil. Good for most solid and liquid airborne particulate hazards that do not contain oil.
- R: Resistant to oil. Can be used in environments with oil-based particles but only for a limited time (typically one shift).
- P: Oil Proof. Can be used in environments with oil and non-oil based particles for longer periods, though filter replacement schedules still apply.
The number tells you the minimum percent filtration efficiency against certain non-oil based particles (for N-series) or against oil and non-oil based particles (for R and P-series) when tested according to NIOSH standards:
- 95: Filters at least 95% of airborne particles. (N95, R95, P95)
- 99: Filters at least 99% of airborne particles. (N99, R99, P99)
- 100: Filters at least 99.97% of airborne particles. (N100, R100, P100) – This is often referred to as HEPA-level filtration.
For many welding applications involving particulate matter (like metal fumes from common welding processes), an N95 respirator might seem sufficient if no oil aerosols are present. However, welding can sometimes produce oily particulates, or cutting fluids might be nearby. Therefore, P-series respirators (P95 or P100) are often recommended for welding because they offer protection against both non-oil and oil-based particles, providing a wider safety margin. A P100 particulate filter offers the highest level of particulate filtration efficiency. Always check the specific weld process and materials; a NIOSH-approved respirator with the correct rating is crucial. Remember, even the best respirator only works if it fits properly and creates a secure seal.
Focus on 3M Disposable Respirators: Are N95 Options like the 8515 Enough?
3M is a well-known name in respiratory protection, offering a wide range of disposable respirators. Many people are familiar with the standard N95 disposable respirator, often used for dust or general particulate protection. But are these standard N95s suitable for welding? Sometimes, but often with limitations. Models like the 3M™ 8515 are marketed as N95 welding respirators. They offer at least 95 percent filtration efficiency against certain non-oil based particles and often include features beneficial for welders, such as flame resistant materials and an exhalation valve (like the 3M™ Cool Flow™ Valve) to reduce heat buildup inside the facepiece.
However, the "N" rating means they are not resistant to oil. If your welding process involves oily particulates (e.g., from cutting fluids, lubricants on the metal, or certain coatings), an N95 respirator might not provide adequate protection over time, as oil can degrade the filter media. Additionally, while N95 filters 95% of particles, some welding fumes contain extremely fine particles, and certain regulations or specific hazards might necessitate a higher level of filtration, like P95 or P100. The 8515 model is often considered suitable for weld applications involving solid particulates where oil isn’t present.
It’s critical to assess the specific welding environment. A standard N95 disposable respirator might be acceptable for light, occasional weld tasks without oil present. But for heavier work, uncertain conditions, or when dealing with more hazardous metals, upgrading to a P-rated respirator (like a P95 or P100) is often the safer choice. These P-rated respirators, whether disposable like the 3M 8212 (P95) or reusable, are approved for environments containing certain oil and non-oil based particles, offering broader protection. Always consult safety data sheets (SDS) for the materials being welded and follow workplace safety guidelines.
Exploring the 3M Particulate Welding Respirator 8212: Why P95?
The 3M Particulate Welding Respirator 8212 is a popular disposable respirator specifically designed with welders in mind. Unlike the N95 models, the 8212 carries a P95 rating. This "P" is significant because it means the respirator provides at least 95 percent filtration efficiency against certain oil and non-oil based particulates. This makes it a more versatile choice for welding environments where oily substances might be present, offering a higher level of confidence compared to an N-rated respirator.
Why choose a P95 like the 8212 over a standard N95 for welding?
- Oil Resistance: Protects even if cutting fluids or oily residues are present.
- Robust Design: Often features cake resistant filter media, which helps the respirator last longer in dusty or fume-heavy environments.
- Welder-Specific Features: The 3M Particulate Welding Respirator 8212 typically includes:
- 3M™ Cool Flow™ Exhalation Valve: Reduces heat and moisture buildup, making the respirator more comfortable to wear for extended periods, especially under a welding helmet. It allows warm, moist breath from inside the respirator to escape easily.
- Adjustable M-noseclip: Helps provide a custom and secure seal against the face, minimizing leaks. This adjustable noseclip is crucial for effectiveness.
- Faceseal: Often includes a comfortable foam face seal or full faceseal for a better fit and increased wearer comfort.
- Flame Resistant: The materials used are designed to resist sparks and flames, an essential safety feature for welding.
- Low-Profile Design: Fits comfortably under most welding helmets and face shields.
The P95 rating provides a solid level of particulate filtration suitable for many common welding applications involving metal fumes. While a P100 offers even higher filtration, the P95 is often considered a good balance of protection, breathability, and cost for a disposable respirator. The 3M™ 8212 respirator helps provide reliable respiratory protection for welders dealing with various particulate hazards.
Do I Need Organic Vapor or Ozone Protection in My Welding Respirator?
While the primary hazard in most welding is particulate matter (metal fumes and dust), some weld processes can also generate harmful gases and vapors, like organic vapor or ozone. Whether you need protection against these depends entirely on the specific materials and processes involved. Standard particulate respirators (N95, P95, P100) are not designed to filter out gases or vapors unless they have an added feature for it.
Organic Vapors: These can be released if you are welding on surfaces that have coatings, paints, solvents, or degreasers containing volatile organic compounds (VOCs). If these substances are heated during weld operations, they can vaporize and become an inhalation hazard. Some disposable respirators, like the 3M 8214 or 8515 models, offer nuisance level organic vapor relief. This means they have a thin layer of activated carbon filter material that can adsorb low concentrations of certain organic vapors, reducing annoying odors. However, they are not suitable for environments where organic vapor concentrations exceed the OSHA PEL or other exposure limits. For significant organic vapor exposure, a reusable half mask or full-face respirator with appropriate organic vapor cartridges is required.
Ozone: Ozone gas is often generated during specific types of welding, particularly MIG and TIG welding on aluminum or stainless steel. Ozone is a lung irritant. Some specialized particulate welding respirators, like the 3M 8214 (N95) or the 8514 (N95), offer ozone protection up to 10 times the OSHA PEL, in addition to particulate filtration and nuisance level organic vapor relief. Again, this protection comes from added filtration layers within the respirator. If significant ozone levels are expected, a respirator specifically rated for ozone is necessary.
In summary, assess your weld process carefully. If you’re only dealing with metal fumes from clean metal, a standard N95 or P95/P100 particulate respirator is likely sufficient. If coatings, cleaners, or specific weld types (like TIG on aluminum) are involved, investigate whether nuisance level organic vapor relief or dedicated ozone protection is needed. A respirator like the 3M 8212 focuses primarily on particulate matter, including oily particles (P95), but doesn’t typically include OV/Ozone layers unless specified in a variant model. Always check the product specifications and limitations.
How Does an Exhalation Valve Improve Respirator Comfort and Performance?
Many disposable and reusable respirators, especially those intended for physically demanding work like welding, feature an exhalation valve. You might wonder what this little plastic piece does and why it’s beneficial. The primary purpose of an exhalation valve is to make breathing out easier and to reduce heat and moisture buildup inside the facepiece. Think of it as a one-way door: it opens when you exhale, allowing your warm, moist breath to escape directly, but closes tightly when you inhale, ensuring that all inhaled air passes through the filter media.
Why is this important, especially for a welder?
- Reduced Heat: Welding generates heat, and wearing a respirator, especially under a welding helmet, can quickly make your face feel hot. The exhalation valve helps release warm air, keeping the inside of the respirator cooler and more comfortable.
- Less Moisture: Your breath contains moisture. Without a valve, this moisture can build up inside the respirator, making it feel damp and uncomfortable. The valve helps vent this moisture, keeping the facepiece drier.
- Easier Breathing: Exhaling through the filter media requires some effort. The valve provides a path of lower resistance for exhaled air, reducing breathing effort and fatigue, particularly during long periods of wear or strenuous activity.
- Prevents Eyewear Fogging: By directing exhaled air downwards and away from the face, a well-designed exhalation valve can help reduce the annoying problem of safety glasses or goggles fogging up.
3M often calls their valve the "Cool Flow™ Valve," highlighting its cooling benefit. While respirators without valves still offer the rated NIOSH-approved protection (like a standard valveless N95), the addition of an exhalation valve significantly enhances wearer comfort. For demanding jobs like welding, this added comfort can mean the difference between wearing the respirator correctly for the entire task versus taking it off due to discomfort, which would negate its protective value. Models like the 3M 8212 (P95) and 8515 (N95) incorporate this feature specifically to improve the welder‘s experience.
Getting the Right Fit: Why is the Adjustable Noseclip and Faceseal So Important?
You can have the best NIOSH-approved respirator in the world, with the highest P100 filtration and a fancy exhalation valve, but if it doesn’t fit your face properly, it won’t protect you effectively. Getting a secure seal between the respirator‘s edge and your skin is absolutely critical. Any gaps allow contaminated air, like welding fumes, to bypass the filter media and enter your lungs. This is where features like an adjustable noseclip and a good faceseal become crucial.
The adjustable noseclip, usually a small metal or plastic strip embedded in the top edge of the respirator, allows you to conform the mask tightly across the bridge of your nose. Noses come in all shapes and sizes, so this adjustability is key to closing potential gaps in this area. A poorly fitting nosepiece is one of the most common reasons for respirator leakage. When putting on a disposable respirator like the 3M 8212 or 8515, you should use both hands to bend the adjustable m-noseclip firmly around your nose to achieve a snug fit. Don’t pinch it with one hand, as this can create angles that break the seal.
The faceseal refers to the part of the respirator edge that contacts your skin. In basic disposable respirators, this might just be the edge of the filter media. However, many welding respirators incorporate a dedicated faceseal, often made of soft foam or a flexible gasket material. This foam face seal provides a cushion against the skin and helps conform to the contours of your face, further improving the secure seal and comfort. Some reusable half facepiece respirators have even more robust silicone or thermoplastic seals. Achieving a custom and secure seal requires both the adjustable noseclip and an effective faceseal working together, along with properly tensioned headband straps. Always perform a user seal check (as per manufacturer instructions) every time you put on your respirator to ensure there are no leaks.
Can I Use a Standard Dust Mask or N95 Respirator for Welding?
This is a common question, and the answer is generally "maybe, but often not recommended." A standard "dust mask" – those flimsy, non-rated masks often sold in hardware stores – offers virtually no protection against the fine particulate matter found in welding fumes. They are designed only for large nuisance dust particles and should never be used for welding respiratory protection.
What about a standard, NIOSH-approved N95 respirator – the kind often used in healthcare or construction? An N95 disposable respirator does filter at least 95 percent filtration efficiency against non-oil based airborne particles. If your welding process only generates non-oil based fumes (e.g., welding clean, uncoated mild steel) and the concentration doesn’t require higher filtration, a basic N95 respirator could theoretically provide adequate particulate protection, provided it fits perfectly.
However, there are significant caveats for welding:
- Oil: Many welding situations involve potential exposure to oily particles (cutting fluids, coatings, etc.). N95 respirators are not resistant to oil, which can degrade their performance. A P-rated respirator (P95 or P100) is safer in these cases.
- Fume Concentration: Some welding processes generate very high concentrations of fumes, potentially exceeding the capacity or protection factor of a basic N95.
- Heat & Sparks: Standard N95 respirators may not be flame resistant. Sparks could potentially ignite or damage the mask material. Welding-specific respirators (like the 3M 8212, 8515, 8214) are designed with this hazard in mind.
- Comfort: Basic N95s often lack features like exhalation valves, which improve comfort during hot, physical work like welding.
- Additional Hazards: Standard N95s offer no protection against organic vapor or ozone, which might be present in some weld scenarios.
Therefore, while a properly fitted N95 might be minimally acceptable in very specific, low-risk welding situations without oil, it’s generally much safer and more practical to use a respirator specifically designed for welding. This usually means a particulate welding respirator with at least a P95 rating (like the 3M 8212) or an N95 with specific welding features (like the 3M 8515 or 8214), including flame resistance, an adjustable noseclip, a good faceseal, and preferably an exhalation valve. Relying on a standard N95 particulate respirator could leave a welder under-protected.
Beyond the Respirator: Considering Helmets, Goggles, and Overall Safety.
Effective respiratory protection from a quality particulate welding respirator is vital, but it’s only one piece of the safety puzzle for a welder. Welding creates multiple hazards, including intense ultraviolet (UV) and infrared (IR) radiation, sparks, heat, and potential impacts. Comprehensive safety requires addressing all these risks.
A welding helmet is essential for protecting the eyes and face from radiation and sparks. Modern auto-darkening helmets provide clear vision before the arc is struck and darken instantly to the correct shade when welding begins. It’s important to choose a respirator that fits comfortably under the chosen welding helmet. Low-profile disposable respirators like the 3M 8212 or 8515, or compact half facepiece reusable respirators, are often designed with helmet compatibility in mind. Ensure there’s no interference that could break the respirator‘s secure seal.
While the helmet protects the face, safety glasses or goggles should often be worn underneath the helmet, especially during grinding or chipping operations associated with weld preparation or cleanup. This provides continuous eye protection even when the helmet is lifted. Again, ensure your eyewear doesn’t interfere with the respirator seal. Other essential personal protective equipment (PPE) includes flame resistant clothing (jacket, apron, pants), leather gloves, and appropriate footwear. Proper ventilation in the workspace is also crucial to reduce the overall concentration of welding fumes in the air, complementing the protection offered by the respirator. A layered approach, combining engineering controls (ventilation), administrative controls (safe work practices), and PPE (respirator, helmet, clothing), provides the best protection.
Maintaining Your Respirator: Tips for Care and Replacement.
Getting the right respirator and ensuring it fits is step one; keeping it effective requires proper care and knowing when to replace it. This applies to both disposable and reusable types.
For disposable respirators (like the 3M 8212 P95 or 8515 N95):
- Inspect Before Use: Always check for damage (tears, holes, crushed areas), missing straps, or a damaged exhalation valve or noseclip. Discard if damaged.
- Handle Carefully: Avoid crushing or excessively folding the respirator, as this can damage the filter media and affect the fit. Store in a clean, dry place away from contaminants when not in use (e.g., during breaks).
- Replace Regularly: Disposable respirators are not meant for extended reuse. Replace them according to manufacturer guidelines or workplace policy, or sooner if:
- Breathing becomes difficult (filter is loaded with particulate).
- The respirator becomes dirty, damaged, or deformed.
- A proper face seal can no longer be achieved.
- It has been used in an environment with high concentrations of fumes. (For P-series used with oil, typically replace after 8 hours or one shift, or per manufacturer guidance).
- Do Not Wash or Clean: Attempting to clean a disposable respirator will damage the filter structure.
For reusable respirators (like a half facepiece reusable respirator):
- Clean the Facepiece: Regularly clean the rubber or silicone facepiece according to manufacturer instructions, usually with mild soap and water or specialized wipes. Ensure it’s completely dry before storing or reattaching filters. Check for cracks, stiffness, or damage. We supply basic cleaning items like Medical cotton swabs which might be useful for careful cleaning of crevices, though specific respirator wipes are often recommended.
- Replace Filters/Cartridges: Particulate filters (P95, P100) need replacing when breathing becomes difficult, they get damaged, or according to a set schedule based on exposure levels. Cartridges for gases/vapors have specific change-out schedules based on exposure and manufacturer data.
- Store Properly: Store the cleaned facepiece and filters in a sealed bag or container away from contaminated areas to protect them.
- Inspect Valves: Regularly check inhalation and exhalation valves for dirt, damage, or distortion. Replace them if necessary.
Proper maintenance ensures your respirator continues to provide the intended level of respiratory protection every time you weld. Neglecting maintenance or overusing a disposable respirator compromises your safety.
Key Takeaways for Welding Respirator Safety:
- Welding Fumes Are Hazardous: They contain fine particles and sometimes gases that require specialized respiratory protection. Standard dust masks are inadequate.
- Choose the Right NIOSH Rating: N95 filters 95% of non-oil particles. P95 filters 95% of oil and non-oil based particles. P100 filters 99.97% of oil and non-oil based particles. P-series (P95, P100) are often safer for welding due to potential oil presence.
- Disposable vs. Reusable: Disposable respirators (e.g., 3M 8212 P95, 8515 N95) are convenient for occasional use. Reusable respirators can be more cost-effective and versatile for frequent welding.
- Fit is Everything: An adjustable noseclip and a good faceseal are crucial for creating a secure seal. No gaps = proper protection. Always perform a user seal check.
- Valves Enhance Comfort: An exhalation valve (like 3M™ Cool Flow™ Valve) reduces heat, moisture, and breathing resistance, making the respirator more comfortable, especially under a welding helmet.
- Consider Added Protection: Check if your process requires nuisance level organic vapor relief or ozone protection beyond standard particulate filtering.
- Use Welding-Specific Respirators: Opt for respirators designed for welding (e.g., 3M Particulate Welding Respirator 8212, 8515) which often feature flame resistance and helmet compatibility.
- Maintain and Replace: Inspect respirators before each use. Replace disposable respirators regularly or when soiled/damaged/breathing becomes hard. Clean and maintain reusable facepieces and replace filters as needed.
- Holistic Safety: Combine your respirator with a welding helmet, eye protection, proper clothing, and good ventilation for overall safety.
Post time: 4月-14-2025